Essential Maintenance Tips for FL/FL3 Positive Displacement Pumps to Extend their Lifespan and Minimal Downtime
February 25, 2025
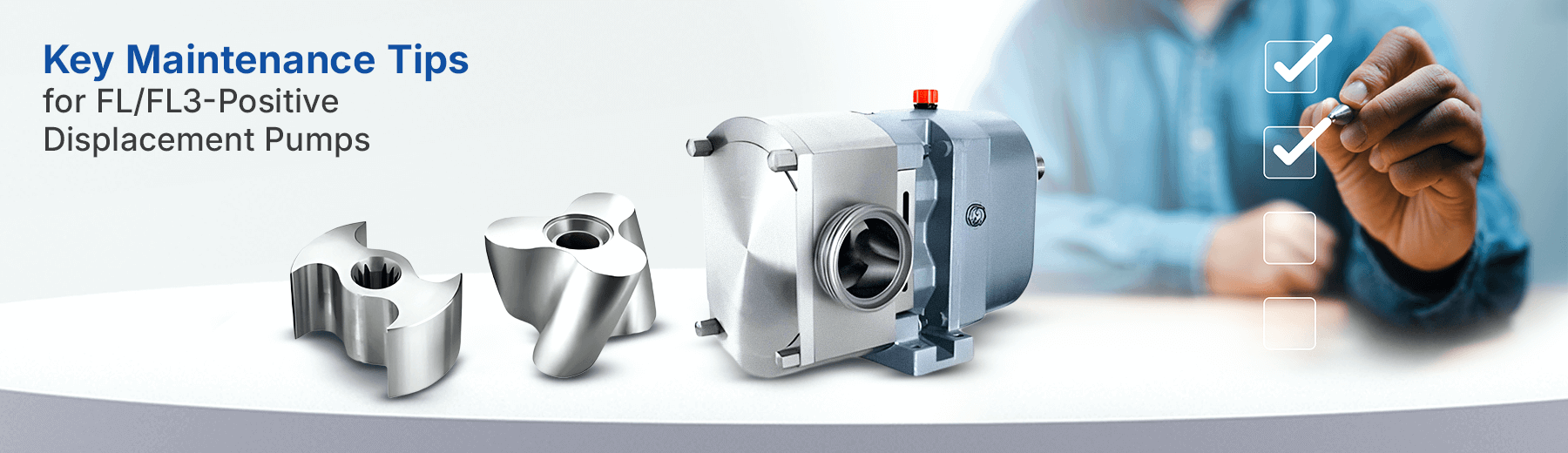
Proper maintenance is essential to keep FL/FL3-Positive Displacement Pumps running efficiently, ensuring a long lifespan and minimal downtime. Since these pumps find extensive applications in dairy, bio-pharmaceutical, and personal care industries where hygiene and reliability are extremely important, maintaining their peak performance would help prevent expensive repairs and avoid any non-conformity of industry standards.
This guide will take you through key maintenance practices to improve the performance of your Positive Displacement Pumps for Industry Applications and maintain them in top condition.
Understanding Positive Displacement Pumps and How They Work
Positive Displacement Pumps' working principle is based on moving a fixed volume of fluid moves through the system with the use of rotating elements like rotors or lobes. This will guarantee a steady flow rate and ensure that they can be applied to any industry that requires precision in handling fluids, even in materials with high viscosity.
Fristam's FL/FL3-Positive Displacement Pumps can handle a variety of products from thin liquids to thick, viscous substances without losing efficiency. Low-slip, contact-free rotors minimize shear stress for gentle and contamination-free product transfer.
Key Maintenance Tips for FL/FL3-Positive Displacement Pumps
Proper maintenance prevents unexpected breakdowns and ensures long-lasting performance. Here's how to take care of your FL/FL3-Positive Displacement Pumps effectively:
1. Oil Level Check (Daily)
Keeping the right oil level is important for the pump to run smoothly. The oil level must be checked every day with the oil sight glass on the side of the gearbox. Proper oil provides the right lubrication to internal parts, avoiding excessive wear and overheating. If the oil level is low, add the recommended lubricant by Fristam to prevent damage to the moving parts of the pump.
2. CIP and SIP Processes
Cleaning and sterilization are essential for pumps employed in industries dealing with food, drinks, and medicines.
CIP (Cleaning in Place): This eliminates impurities without dismantling the pump. The cleaning cycle includes:
- A preliminary flush with water.
- A caustic flush with NaOH (1%-2%) at 80–85°C.
- An intermediate flush with water.
- An acid flush using HNO3 (1%) at 60–65°C.
- A final water flush.
The pump’s differential pressure should be 2–3 bar to ensure proper flow rates.
SIP (Sterilization in Place): This method ensures pump sterilization, but it must have prior approval from Fristam. It is only applicable to pumps that have suitable elastomers. The maximum process temperature is 145°C, and varying temperature ratings may be different for ATEX operations.
3. Inspection of Sealing and Quenching Liquid (Daily, if any)
For pumps that have a sealing or quenching liquid system, the system should be inspected daily. This liquid ensures leak prevention and easy running.
- Verify the sealing liquid head and cross-check with the value indicated in the order documents.
- Maintain the liquid temperature below 70°C in operation since excessive heat may degrade the seal's performance.
Regular monitoring helps prevent leaks and contamination of the pumped product.
4. Oil Change (Every 2,000–4,000 Hours)
Periodic oil changes guarantee lubrication to an optimal level and avoid wear.
- In severe operating conditions (aggressive environments, high humidity, or temperature variations), replace the oil every 2,000 hours.
- In regular conditions, replace the oil every 4,000 hours or yearly.
Use only the manufacturer-recommended lubricant to ensure the pump’s longevity.
5. Shaft Seal Replacement (When Necessary)
The shaft seal maintains leak prevention and contamination prevention. Replace it immediately if:
- Pumping medium or sealing/quenching liquid leaks from the pump.
- Sealing or quenching liquid gets mixed in the pumped product and contaminates it.
Regular inspection ensures early detection of wear, avoiding possible failures.
6. Coupling Replacement (As Needed)
The coupling links the pump to the motor and provides effective power transmission. A faulty or out-of-alignment coupling will produce vibration, noise, and low efficiency.
- Use only manufactured approved couplings to avoid performance problems.
- Replace the coupling as soon as some wear or misalignment occurs to prevent continued damage to the pump and motor.
7. Gear Motor Replacement (As Needed)
The gear motor drives the pump and needs to be in proper condition to ensure efficiency. If the motor indicates impending failure, overheating, or inefficiency, replace it immediately.
- For FKF models, contact Fristam for the correct replacement procedure.
- Ensure proper coupling alignment during installation to avoid operational issues.
8. Lubrication of Motor Bearings (As Per Manufacturer’s Guidelines)
Proper lubrication of motor bearings reduces friction, prevents overheating, and extends motor life.
- Follow the manufacturer’s lubrication schedule.
- Use the recommended lubricant alone to ensure the best performance.
Not lubricating the bearings may result in premature wear, noise, and eventual failure.
9. Regular Cleaning and Debris Removal
Clogging and loss of efficiency may result from dirt and debris. Cleaning regularly guarantees free movement.
- Remove foreign objects from the pump and piping system before sealing the pump.
- Only use approved cleaning substances that satisfy hygiene standards for the pumped medium.
- Clean the pump and pipe system extensively prior to the first operation to avoid contamination.
10. Periodic Clearance Adjustment
The clearances need to be checked and adjusted to facilitate free movement of the rotor.
- Clearance needs to be checked whenever shaft bearings or rotors are renewed.
- Measure the axial clearance using a feeler gauge. The suggested clearance is 0.04–0.08 mm to guarantee smooth operation.
Excessive wear, noise, and low performance can be caused by incorrect clearance.
11. Follow the Manufacturer's Recommended Maintenance Schedulet
Every pump model has unique maintenance needs specified by the manufacturer.
- Maintain a maintenance log to record servicing intervals.
- Adhere to Fristam's guidelines for replacement, lubrication, and inspections.
Compliance with the manufacturer's maintenance schedule ensures maximum efficiency, minimal downtime, and prolonged pump life.
Key Takeaways
To maintain the longevity of FL/FL3-Positive Displacement Pumps, proper and regular maintenance is necessary. With these maintenance tips, you can avoid all the costly breakdowns, increase efficiency, and maintain compliance with hygiene standards.
Fristam Pumps is a leading Positive Displacement Pumps manufacturer in India, it offers industry-leading solutions for precise and hygienic fluid handling. For information on our Positive Displacement Pumps for Industry Applications, visit our website today.
1. What is the importance of checking the oil level daily in FL/FL3 pumps?
Monitoring the oil level daily maintains the right lubrication, avoids overheating, minimizes wear, and prolongs pump life by avoiding unnecessary breakdowns caused by incorrect lubrication.
2. How often should the oil in FL/FL3 pumps be changed?
Under normal conditions, replace the oil every 4,000 operating hours or annually. Under harsh operating conditions, replace it every 2,000 operating hours for optimal performance.
3. What are the recommended cleaning procedures for FL/FL3 pumps?
Use the CIP (Cleaning in Place) procedure: water rinse, NaOH (80-85°C) clean, rinse, HNO3 (60-65°C) rinse, and final rinse for hygienic and effective operation.